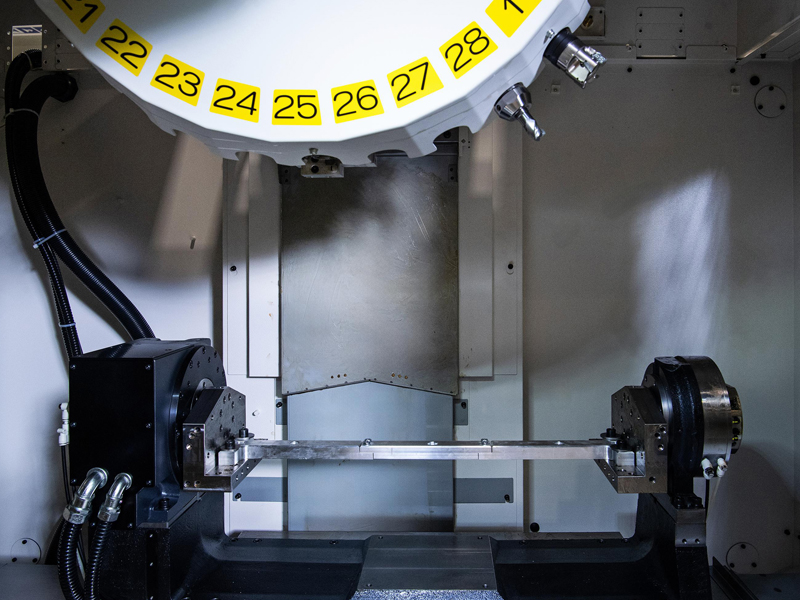
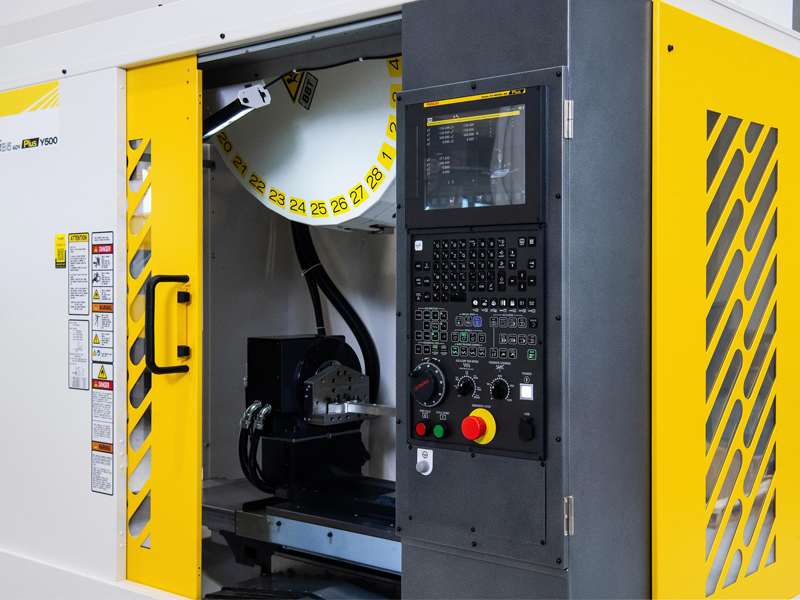
FANUC, which pioneers the development of CNC controllers, robots and machines in the automation industry, has added two advanced models to its product range. With the possibility of direct sales by FANUC Turkey, ROBODRILL α-D28LiB5ADV Plus Y500 and ROBODRILL α-D28MiB5ADV Plus especially help electric vehicle manufacturers to process large parts and gain competitive profits.
Japan-based CNC, robot and machine manufacturer FANUC continues to increase the model range of ROBODRILL, the new generation vertical machining center that offers unrivaled versatility, and added ROBODRILL α-D28LiB5ADV Plus Y500 and ROBODRILL α-D28MiB5ADV Plus to its portfolio. The α-D28LiB5ADV Plus Y500 provides an extended 500mm Y-axis so customers can apply ROBODRILL’s superior precision and speed to larger components, while the ADV Plus includes a larger 28-station automatic tool changer (ATC) while retaining the standard 400mm Y-axis Featuring a number of upgrades shared with the Y500, ROBODRILL α-D28MiB5ADV Plus offers FANC’s latest 31i-B5 Plus control.

High productivity in the automotive arena with rapid tool changes
Featuring a larger table that can carry loads of up to 400 kg, the new ROBODRILL α-D28LiB5ADV Plus Y500, with its 500 mm Y-axis, covers a number of large components common in industries such as automotive, especially in the electric vehicle (EV) segment. Combined with an extended table depth of 500 mm to accommodate larger fixtures, the new machine offers the ideal solution for parts such as electric vehicle battery cases and inverter cases. Offering unrivaled versatility, the latest model supports shorter cycle times in drilling and tapping by offering higher traverse speeds (up to 60 m/min) and acceleration (2.2 G) in the Z-axis. Another innovation is the addition of a 28-station ATC (from the standard 21), which can carry a total tool weight of up to 46 kg and offers a fast tool change speed of 0.7 seconds (from tool to tool). Greater tool availability thus allows users to handle a wider range of machining tasks involving larger workpieces, while rapid tool changes encourage gains in productivity, a vital metric in the high-volume automotive arena.
FANUC’s latest 31i-B5 Plus control in α-D28MiB5ADV Plus
Another new model in the series, the ROBODRILL α-D28MiB5ADV Plus, although it does not have the extended Y-axis, has 28-station ATC and a maximum table load of 400 kg, as well as FANUC’s latest 31i-B5 Plus control for multi-axis, high-speed, high-precision machining . When it comes to connectivity, both models support all major industrial communications protocols to ensure customers can access the many benefits of real-time production monitoring and data analysis. All the usual FANUC options for spindle speed (up to 24,000 rpm) and number of axes (3, 4 or 5) are included in both new models, thanks to high-performance rotary tables and trunnion units, as well as easy, single-cable connection between robot and machine makes it possible to realize any ROBODRILL investment through its comprehensive portfolio of industrial robots and cobots.