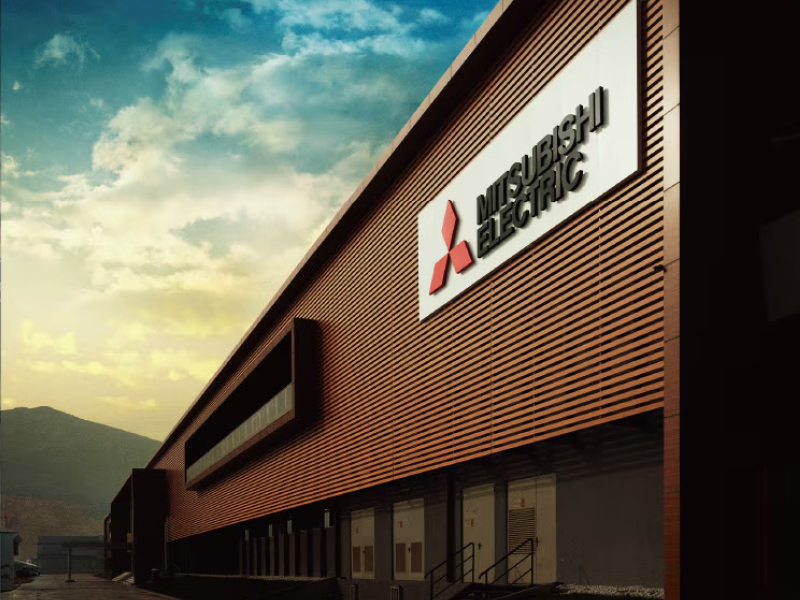
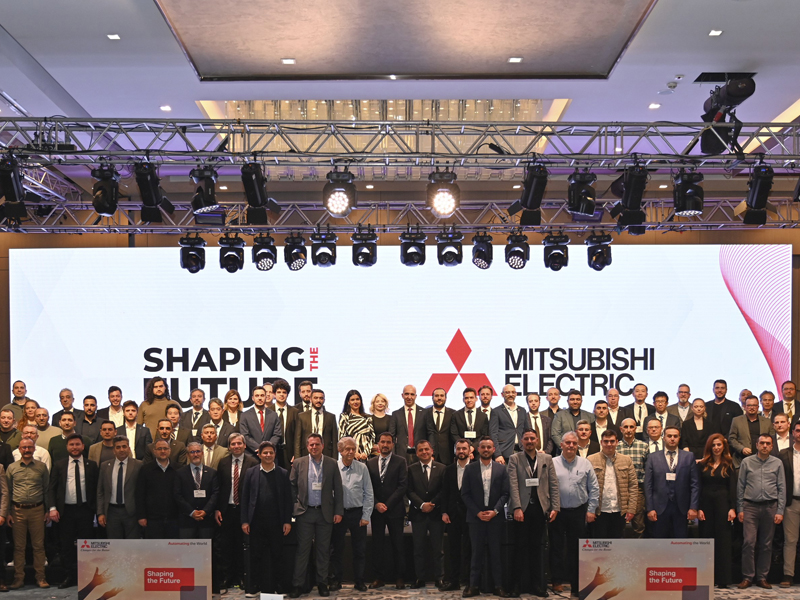
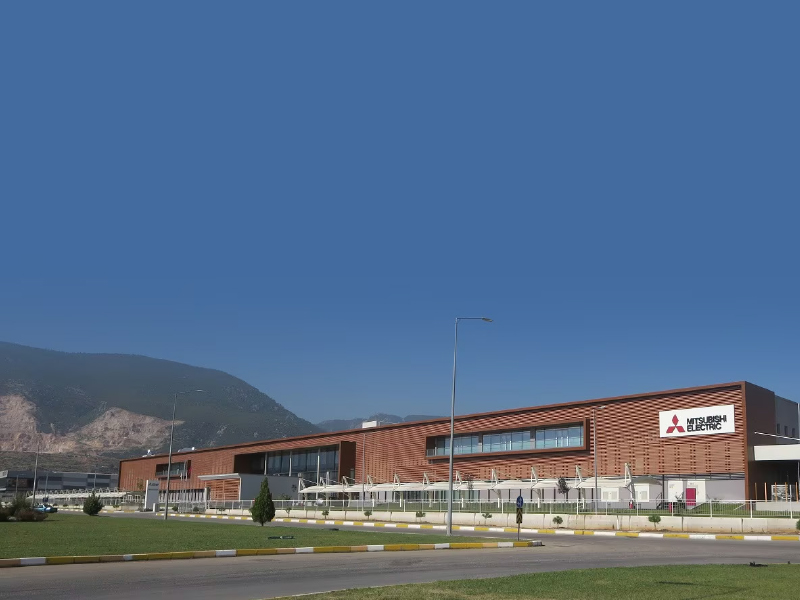
Mitsubishi Electric, one of the world's leading CNC manufacturers, introduced the M8V CNC series, the updated version of the M8 series, at the "Shaping The Future" themed launch held in Istanbul. The new M8V CNC series provides nearly 12% improvement in cycle times compared to the previous series; It opens the doors of a new world to businesses with its standard advantages such as drag and drop, multi-touch, WLAN wireless network features, new generation technologies, higher speed and surface sensitivity.
Mitsubishi Electric Turkey Factory Automation Systems introduced its new M8V CNC series, which is a game-changer in the CNC field, at the launch organized in Istanbul with the theme "Shaping The Future". The launch, hosted by Mitsubishi Electric Turkey Vice President Jun Horibe and Mitsubishi Electric Turkey Factory Automation Systems General Manager Nurettin Geçgel, was attended by Mitsubishi Electric Europe CNC Department Manager Jun Odawara, Mitsubishi Electric Corporation Business Development Department Senior Manager Ito Yuhi and Mitsubishi Electric Turkey Factory Automation Systems Manager. Systems started with the opening speeches of Mechatronics CNC Department Manager Hakan Aydın. Comprehensive information was given about the series, which has the first integrated Wi-Fi in its field as of July 2021, when it was first introduced, and offers high performance with its intuitive and easy-to-use interface. With the M8V CNC series, which combines flexibility with functionality and new technologies, manufacturers have the opportunity to work faster and more efficiently and have higher productivity and profitability.
In his opening speech at the launch, Mitsubishi Electric Turkey Factory Automation Systems General Manager Nurettin Geçgel said, “As Mitsubishi Electric, in addition to being one of the world's largest CNC manufacturers, we are also a strong solution partner of successful machine tool manufacturers in the world and in Turkey. We provide professional service and spare parts for machines equipped with Mitsubishi Electric CNC products. Our innovative control technology; With our CNC technologies based on high quality, usability and network communication, we bring high product quality to the industry in Turkey as well as around the world. With our CNC technologies that we have developed in the light of our deep-rooted history of innovation, we offer more and more added value to manufacturers for CNC machining centers, CNC lathes and CNC laser machines. "Our new M8V CNC series, which we developed to support manufacturers' digital transformation strategies and can be used as easily as smart devices, makes the work of professionals in different fields of industry easier and provides flexibility to users with its unique design," he said.

Flexible and fast production cycle with high precision, high surface quality and shorter cycle times
Hakan Aydın, Mitsubishi Electric Factory Automation Systems Mechatronics CNC Department Manager, emphasized in his speech that the M8V series is equipped with much more up-to-date technologies compared to the previous series, and said: "The CPU designed for CNC, brought together in the new series, provides both high and high performance with its innovative OMR-CC control technology and automatic cutting load control." It provides a high level of precision and shortens cycle times. In these days when smart factories and Industry 4.0 are turning into a necessity, the new M8V CNC series, which offers technologies such as easy connection, direct robot control and Remote4u as standard, also improves cycle times by approximately 12 percent compared to previous models. In addition, it can automatically tolerate CAM-induced tool path errors up to approximately 15 percent compared to the previous series. "The new series also offers higher speed, precision, surface quality, longer tool life and shorter cycle times in metal processing, with the number of front reading blocks doubled compared to the previous generation." Aydın added that thanks to the new intuitive design, frequently performed operations such as workpiece programming and tool management, especially the cutting conditions parameters that affect the surface quality, can be adjusted much more easily and quickly.
