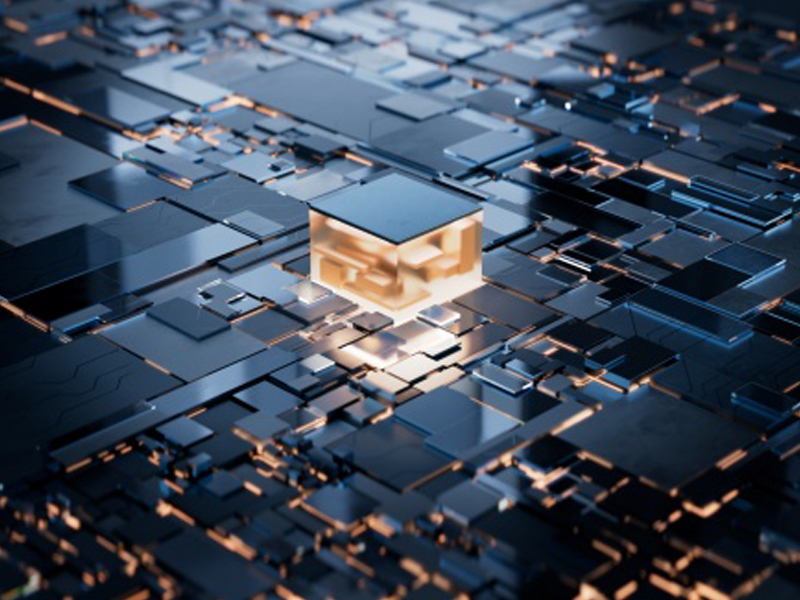
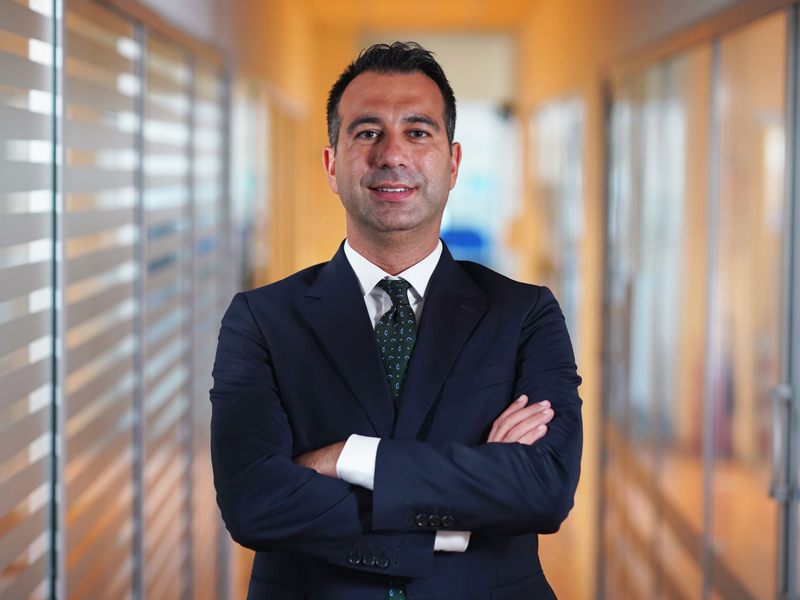
Atlas Copco Compressor Technique; With the heat recycling application it implements in the compressors it offers to the industry, it saves approximately 1.1 million TL of energy per compressor per year. Atlas Copco Compressor Technical Service Department Manager Özgün Şenol said that a total of 6,600,000/kWh of energy was saved with the heat recycling practices they carried out last year.
Atlas Copco Compressor Technology, which has been serving industrial enterprises in Turkey for 71 years, provides energy savings of approximately 1.1 million lira per compressor annually through heat recycling.
Atlas Copco Compressor Technical Service Department Manager Özgün Şenol said that although the amount of savings varies depending on the capacity of the compressor, a total of 6 million 600 thousand kWh of energy was saved with the heat recycling application they implemented in oil screw compressors last year. Şenol gave the following information about energy saving: “When we take the electricity unit price as the average market value of 0.1 €/kWh, the total amount of savings we achieve in a year reaches 660 thousand euros. This corresponds to approximately 23 million lira. “We save an average of 1 million 100 thousand TL annually per compressor.”

Simple and fast project that businesses can do to reduce carbon
Özgün Şenol stated that they carried out feasibility studies with field visits and long-term measurements to determine the compressors to be applied and said, “Here, savings amounts are studied through preliminary savings reports, instant measurements or simulation of long-term measurements. It should always be remembered that these projects are energy efficiency projects. Generally, the repayment period is less than 1 year. "It is one of the simplest and fastest projects that can be implemented in carbon emission reduction, which is the responsibility of every business," he said.
“Hot water is obtained up to 75 degrees”
According to the information given by Özgün Şenol about the energy recycling technique with compressors, in oil screw compressors, most of the heat released by the compression of the air passes into the oil and an energy recycling is achieved by obtaining hot water up to 75 degrees from this hot oil. This is achieved with the help of a unit added to the compressor.
In oil-free screw compressors, the hot water that rotates inside the compressor and takes on the waste heat, not from oil, is provided by a unit that will rearrange the compressor circuit elements and heat the water to be used in the operation. Likewise, in this application, hot water up to 75 degrees is obtained.
“We offer heat recycling service as a project”
Özgün Şenol stated that they offer the heat recycling application to customers as a project, not a product, and that they provide consultancy on where the hot water will be used, the design of hot water lines and what to pay attention to.
Atlas Copco Compressor Technique aims to increase the energy savings achieved by this application in the industry by 50 percent by implementing heat recovery with both oil and oil-free compressors in 2024.