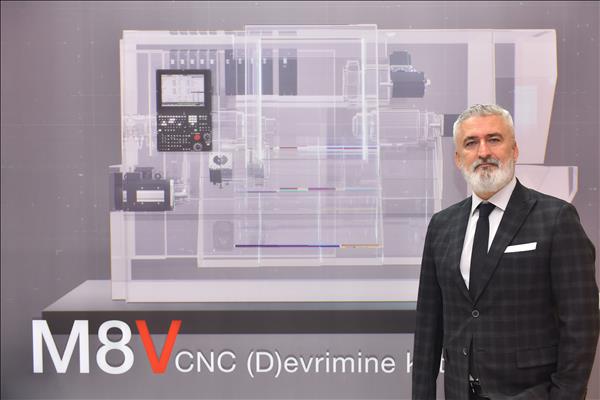
Mitsubishi Electric, one of the largest CNC technology manufacturers in the world, is breaking the ground in the field of CNC with its new M8V series, which combines flexibility with functionality. The possibilities of this new series provide faster and smoother operation, higher productivity and profitability. The series, which is completely based on convenience, offers a user experience similar to using a smartphone with its interactive panel interface that supports four-point multi-touch hand gestures.
Developing CNC technologies that pave the way for mass production in the light of its deep-rooted innovation history, Mitsubishi Electric increases the added value it offers to manufacturers for CNC machining centers and lathes day by day. Finally, the company, which brings the new M8V series, which attracts attention with its practical use, to the manufacturers, aims to make its production processes error-free and sustainable with high efficiency and precision. Talking about the features of the series, which is the first and only in its field with built-in Wi-Fi, and offers superior performance with its intuitive and easy-to-use interface, Mitsubishi Electric Factory Automation Systems Mechatronics CNC Department Manager Hakan Aydın made important statements about the new controllers, which are much more effective than the previous series. .
Flexible and fast period in production with maximum accessibility
Talking about the new M8V, which plays a key role in realizing the advanced Industrial Internet of Things (IIoT) for data-driven smart manufacturing, Hakan Aydın said; “This series was developed to support manufacturers’ digital transformation strategies. The new series, which facilitates the work of professionals in different fields of activity of the industry, provides users with perfect flexibility with its original design.
Users can safely monitor CNC machine tools from anywhere and anytime with the help of connected devices such as tablets. The intuitive design of the series helps to monitor and control key manufacturing parameters easily. The Job Lathe wizard, which guides the users during the installation, provides an easy and fast programming opportunity. With this feature, it stands out as a controller that even personnel who do not have G-code expertise can interact with easily.”
Reduces production time, provides high level of precision
Pointing out that the new series is much more effective and efficient than the previous generation, Hakan Aydın said; “The CPU, innovative OMR-CC control technology and automatic shear load control combined in the new series provide a high level of precision while reducing fabrication time. Supporting high quality production, these functions reduce cycle time by at least 11 percent and tool path errors by up to 15 percent compared to previous models. The M8V series also offers significant advantages to metalworking applications thanks to its high number of axles in machining centers and its doubled finishing capacity of 540 kilo-block codes per minute. Combining speed and performance, this controller series helps manufacturers implement smart manufacturing applications while increasing their efficiency.”