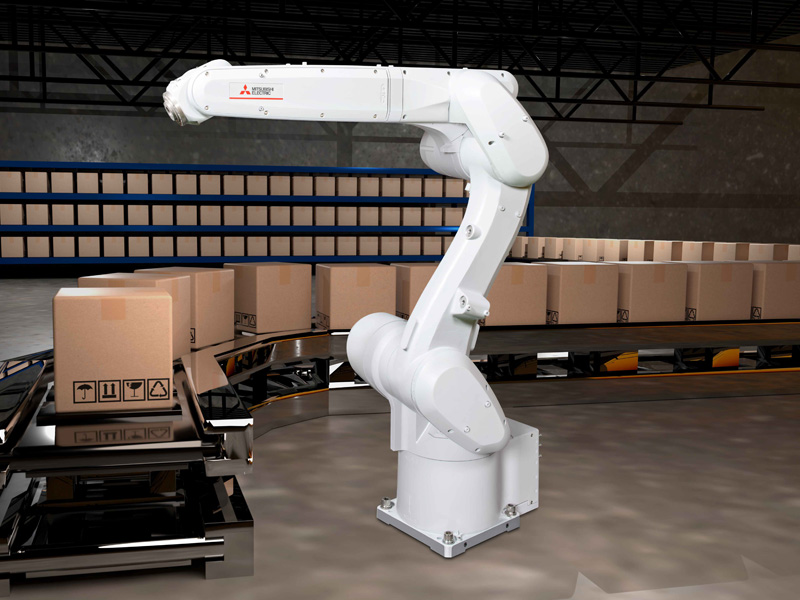
Mitsubishi Electric’s MELFA SafePlus robot safety technology brings a new level of human-machine collaboration to the manufacturing industry as demand for robotic solutions increases rapidly. MELFA SafePlus transforms the company’s more than 160 intelligent industrial robot models in the MELFA FR series into collaborative systems that do not require safety cages, making them safer, easier to use and more efficient.
In today’s world where human-machine interactions have reached a complex stage, it is of great importance that robots can work safely with human operators without the use of cages. The fact that robots work in harmony and effectively with humans eliminates safety barriers and maximizes space utilization in factories, increasing the efficiency of production cells.
Mitsubishi Electric’s MELFA SafePlus robot safety solution takes production processes to the next level with the company’s more than 160 intelligent industrial robot models in the MELFA FR series. Applicable to both horizontal SCARA and vertical articulated arms, MELFA SafePlus offers safety monitoring fun
ctions capable of adapting to various conditions. Thanks to this solution, robots connected to Melfa Safe Plus with safety sensors can work in a certain area (Safety Limited Position) or increase their speed to a safe point (Safety Limited Speed) and provide safe stops, depending on the presence of people. When the violation in the area is eliminated, the robot can gradually start working from where it left off. In this way, violation errors are eliminated, the robot’s safe start scenarios are automated, and the machine’s working times are improved and productivity is increased.
A new era in reliability and flexibility
The latest version of SafePlus offers functions such as safety logic editing, speed and position monitoring, which further increase safety performance, in addition to the safety monitoring and collision detection features required for collaborative operations. In the previous version, it determined a cubic speed monitoring area with equal x, y and z safety distances, allowing the robot to reduce its speed when operators were in this area. With its new version, SafePlus now allows the creation of asymmetric areas with different safety distances. By significantly reducing the safe distances in the directions where the robot is not moving, emergency stop interruptions can be safely reduced and applications can be made in narrower spaces. End users have the flexibility to easily create and operate safety systems that are suitable for the intended applications. Safety monitoring conditions and operating parameters can be configured directly in the robot controller without the need for dedicated safety CPUs.
Mitsubishi Electric has increased the number of copy-safe I/O inputs and outputs in the system to create more reliable and flexible safety systems. MELFA SafePlus uses safety measures certified by the leading independent certification body TÜV SÜD to ensure compliance with international IEC and EN standards such as EN 61800-5-2 for safe movement and EN 60204 for safe stopping.