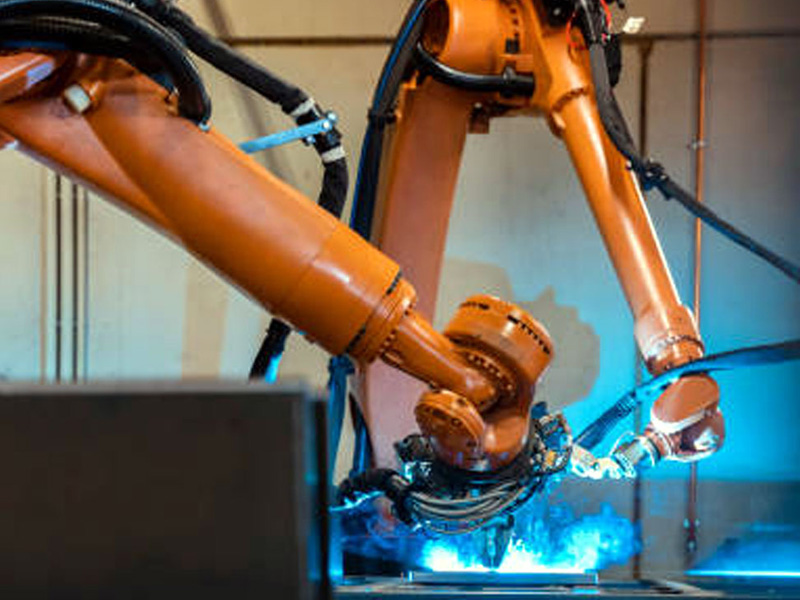
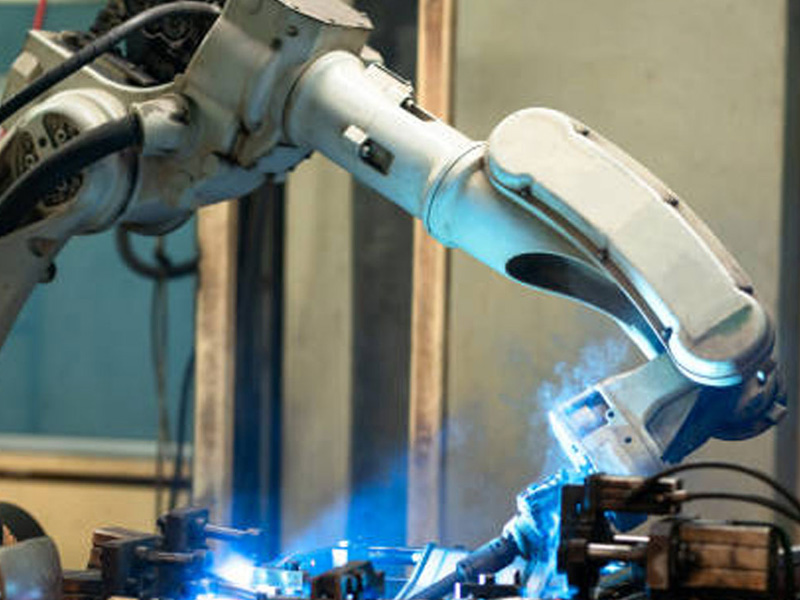
Vega Makina, which supplies welding technologies to industrial establishments operating in all sectors, brings businesses together with efficiency with its WeldBOX-M Robotic Arc Welding Systems and WeldBOX-L Robotic Laser Welding Systems. WeldBOX-M and WeldBOX-L, which have high flexibility with their robotic infrastructure, increase employee safety and minimize errors in work processes.
Serving with welding and cutting machines, laser welding machines, welding generators, welding wires, hard solder wires and welding consumables in its product range, Vega Makina brings industrialists together with the most up-to-date technologies. Raising quality standards with its robotic arc welding and laser welding systems, the company makes work processes in narrow areas practical.
The password for quality and consistency in production: WeldBOX-M
Designed to provide higher quality and more efficient production by reducing labor costs, minimize welding errors, increase production speed and help achieve competitive advantage by reducing operating costs, WeldBOX-M Robotic Arc Welding Systems also offer advantages such as flexible movement in narrow spaces. Allowing the workforce to be directed to more creative and strategic tasks by taking the repetitive workload off employees, WeldBOX-M helps produce high quality and error-free products by minimizing the margin of error in production processes.

The programmable structure of the system, which has the ability to adapt to different welding techniques and materials, can be quickly configured for new workpieces, while minimizing material waste thanks to more precise welding processes.
Ahead in competition without compromising quality with WeldBOX-L
Combining the advantages of laser welding with the precision and automation of robot technology, WeldBOX-L Robotic Laser Welding Systems reduce the completion time of the job without compromising quality. Optimizing the workforce and increasing quality standards by automating the welding process, WeldBOX-L enables more efficient production thanks to its automation and fast welding capabilities. The system, which increases production speed by minimizing welding errors and thus reduces operating costs, provides competitive advantage with time and cost savings.
Every step of production is monitored with software
Optimizing the workforce and increasing quality standards by automating the welding process, WeldBOX-M and WeldBOX-L can weld with high precision. Since it provides more efficient production thanks to its automation and fast welding capabilities, it also provides industrialists with time and cost savings. The system makes production monitoring flawless with ‘source monitoring’, which provides opportunities to monitor the operation and record data, detect errors and improve them, ‘quality control’, which optimizes the production process, and ‘data analysis and reporting’, which provides an overview of the business. Thanks to the system, the entire process from the first step of production to the last step, where the quality of the manufactured product is determined, can be monitored with superior software.