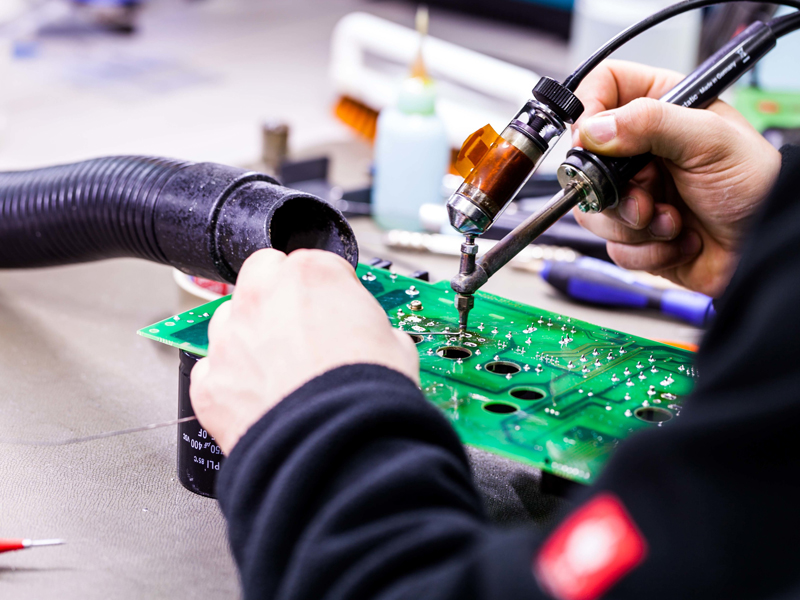
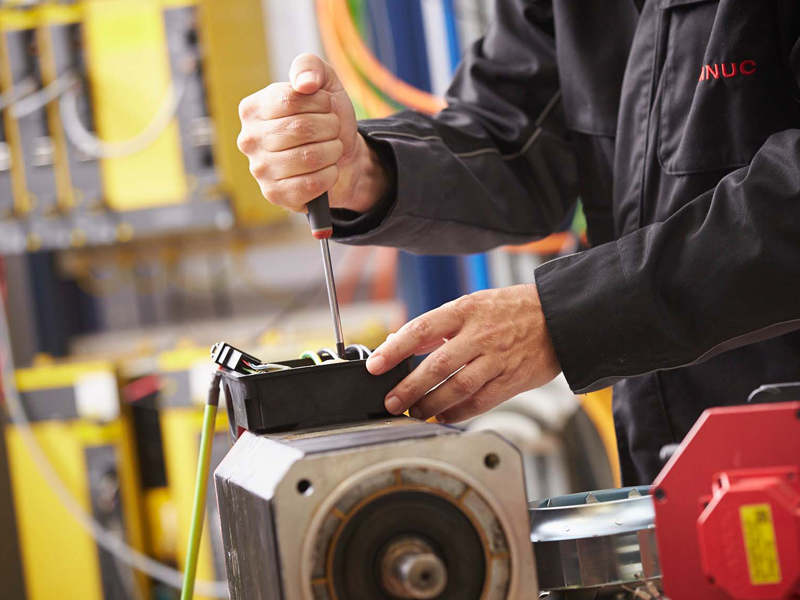
The Repair Center, which FANUC, one of the world’s leading factory automation manufacturers, established in Turkey four years ago with an investment budget of 250 thousand Euros, ensures sustainable after-sales service quality. While the center is FANUC’s second repair point in Europe, companies meet with unrivaled quality thanks to servo motor, spindle motor, teach pendant and finally drive repair offered.
FANUC, which is working to expand the capacity of the center, which promises 100 percent original spare parts and high precision guarantee as well as a one-year repair (renewal) warranty, will increase the capacity of the existing Repair Center by 5 times within the new factory investment it will open in Sancaktepe this year.
In the Repair Center opened in 2020 within the scope of Japan-based CNC, robot and machine manufacturer FANUC’s long-term strategy in Turkey, the fault detection, repair and delivery of the products are carried out in the fastest way by expert teams, while after-sales service assurance is provided. The center, which serves in an area of 500 square meters and has the same concept as FANUC’s Repair Center in Europe, repairs products such as servo motors, cards and teach pendants in FANUC robots, in addition to servo motors, drivers and card products in CNC machines. Drive repair, newly launched at the center, offers unrivaled expertise in the repair and renewal of servo and spindle drives and FANUC robot servo drives.
Professional, fast and economical repair service in FANUC quality
Stating that factory automation and robot investments form a whole with after-sales service, FANUC Turkey General Manager Teoman Alper Yiğit said, “After-sales service has an important role in ensuring that companies get the reward of their high investments in automation and make their productivity sustainable.

As FANUC, we support the industry and produce comprehensive solutions with after-sales services such as service, maintenance, training and retrofit that we offer to companies in Turkey. The FANUC Türkiye Repair Center, which we put into service in line with this understanding, also causes loss of time and cost, and is unprofessional.Instead of remote solutions, it offers FANUC quality professional, fast and economical repair service. “In addition, our customers minimize their losses in production and increase their efficiency and profits.”
100 percent original spare parts guarantee
Stating that they guarantee minimum downtime thanks to the rapid detection, offer, repair and delivery process, Yiğit said the following about the advantages they offer: “In our center, we guarantee unrivaled quality as well as competitive prices.
As a matter of fact, we repair the product with the updates and improvements specified by the original manufacturer. At this point, the use of 100 percent original spare parts is an essential part of our repair process. Our technical team uses specialized testing equipment and not only repairs, but also performs automatic cleaning and painting. We deliver the products we repair, refurbished, brand new in their box, with a one-year product warranty. Our aim is to make FANUC quality sustainable at the time of sale and during the period of use, as well as in the after-sales process.”
FANUC Türkiye Repair Center increases its capacity by 5 times
Stating that the capacity increase was made for FANUC Turkey Repair Center to provide a higher level of service, Yiğit said, “Our capacity will increase significantly with the new factory and technology center that we plan to commission in Sancaktepe this year. Our Repair Center will have a volume and capacity 5 times larger in our new building, which will start operating in order to produce the most suitable solution for our customers’ needs and to enable them to get ahead in global competition. “In this way, we will serve many more customers at the same time and offer FANUC quality without interruption,” he said.