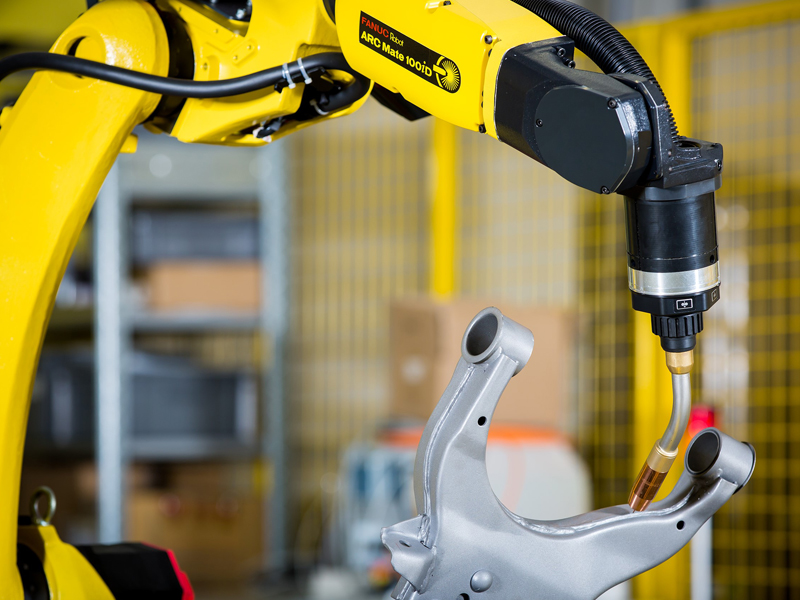
ARC Mate series robots, offered to industrialists as a product of many years of experience by FANUC, the leading leader of numerical control systems in the world markets, enable a payload of up to 35 kg and a reach of up to 2 m. ARC Mate, which is specially designed by FANUC for arc welding and has many models for different needs, guarantees accuracy and repeatability in all applications.
Offering a variety of solutions according to different user expectations, Japan-based FANUC carries out arc welding, spot welding and laser welding as well as cutting applications with more precise performance with the ARC Mate series robots specially designed for arc welding. Featuring different models that meet a wide range of demands, the series is offered with a variety of tools to increase versatility and help make processes more efficient.
Compatible with welding applications in many industries with its slim wrist design
Thanks to its thin arm and hollow wrist design, FANUC ARC Mate series robots can reach the narrowest spaces as well as carry very heavy loads. While its thin wrist design makes it ideal for use in different sectors, it is used extensively in the automotive industry, especially as TIER 1 for welded seats, axles and other parts. While the robot’s structure allows it to access narrow spaces, it also reduces costs by minimizing wear and tear on the welding wires. Offline programming makes it easier to foresee contact problems that may occur during the welding process. Providing flawless communication for all leading power supplies, the series also minimizes integration and installation time. The ARC Mate series has a high-level digital interface for the widest range of power supply brands, thus helping to directly monitor and adjust the power supply welding parameters with the Robot iPendant. The robots in the series work with a high success rate in locating parts and welding locations, as well as identifying part types and providing post-welding checks, with iRVision technology, which has a unique vision system. TorchMate technology increases welding efficiency by automatically adjusting the Tool Center Point (TCP) and eliminating the time-consuming reteaching process caused by torch or wire deflections following collisions.